Did You Know That Even Skilled Pilots Often Made Mistakes Before the Age of Ergonomics?
Imagine stepping into the cockpit of a vintage aircraft in the early 20th century. You’re an experienced pilot, trained in navigation, weather interpretation, and emergency procedures. You have thousands of hours of flight time, yet the simplest of errors—misreading a dial, flipping the wrong switch, or failing to notice a crucial warning light—could lead to disaster.
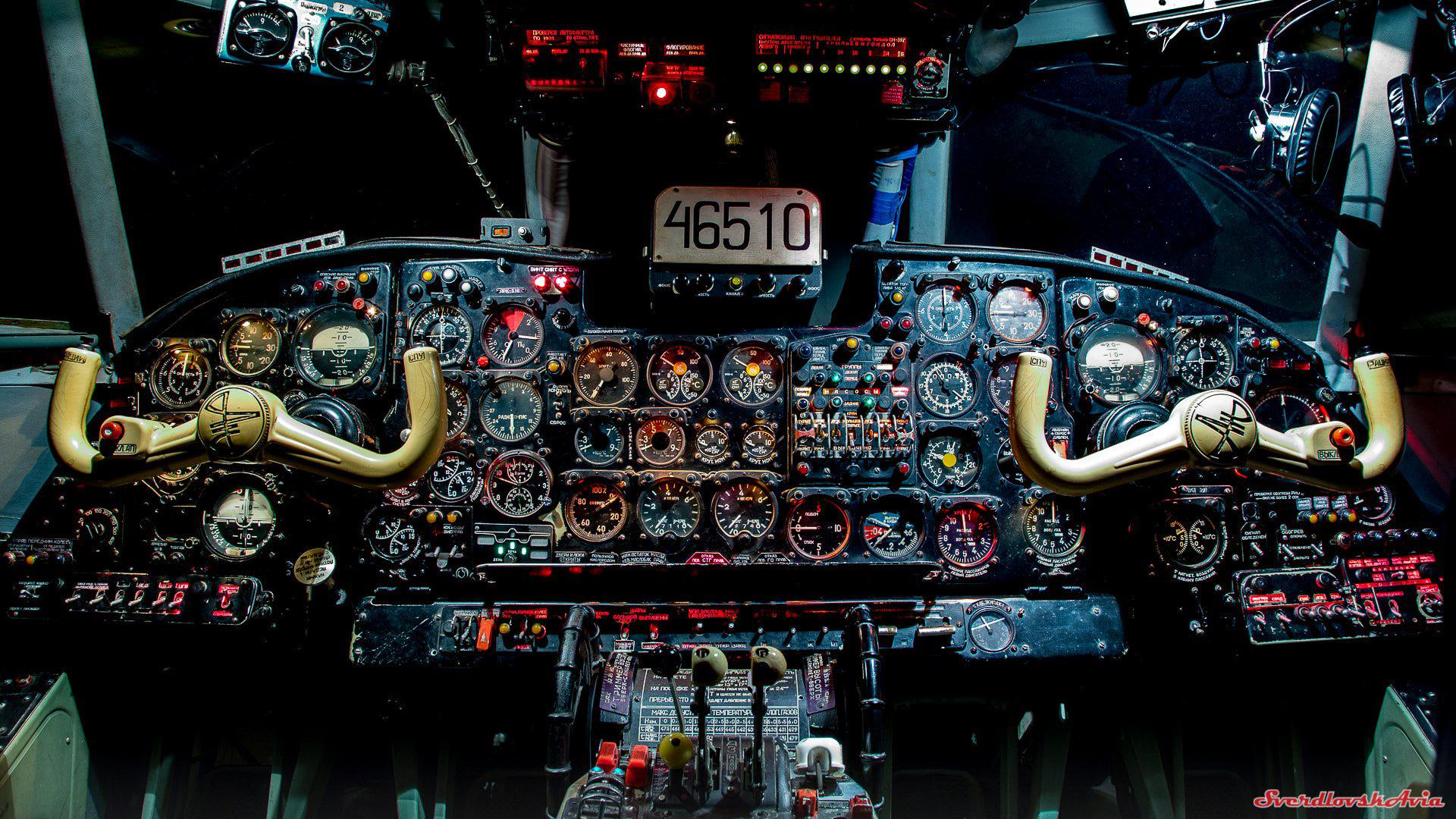
This wasn’t just bad luck. It was a direct result of poorly designed cockpit layouts, confusing controls, and overwhelming workloads. Before the rise of ergonomics and human factors engineering, even the most skilled pilots were prone to errors—not because they were incompetent, but because their environment worked against them.
The Problem: Cockpit Chaos
In the early days of aviation, airplane cockpits were an unorganized mess. Controls, dials, and switches were placed wherever the engineers thought they would fit, with little consideration for human psychology or physical limitations.
During World War II, a significant number of crashes were attributed not to mechanical failure or enemy fire but to pilot error. One notorious problem was the confusion between the landing gear lever and the flap control lever. In many aircraft, these two essential controls were nearly identical in shape, size, and location. Pilots, under pressure and operating at high speeds, would sometimes retract the landing gear instead of adjusting the flaps, leading to catastrophic accidents.
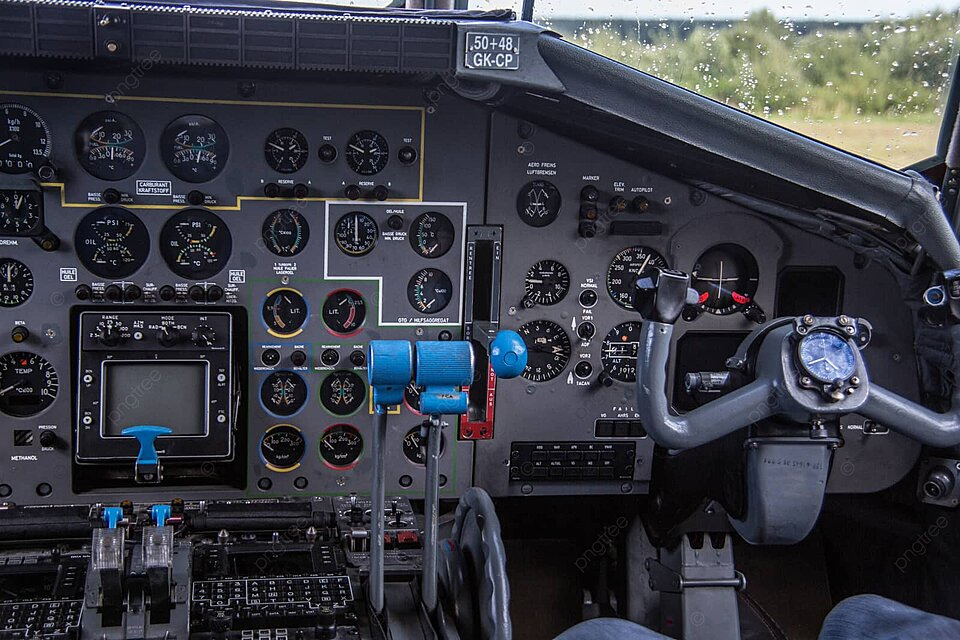
The Human Brain vs. Bad Design
Humans are not perfect machines. Our brains rely on patterns, muscle memory, and instinctual responses. Under stress, we tend to revert to habits, which means if two controls feel the same, look similar, and are positioned close to each other, a mistake is inevitable.
Consider this: You’re typing on a keyboard, and someone suddenly rearranges the keys. Your fingers instinctively press where the letters should be, not where they now are. The result? Chaos. This is exactly what pilots faced in poorly designed cockpits—except the consequences were far worse than a misspelled word.
Enter Ergonomics: A Game Changer for Aviation
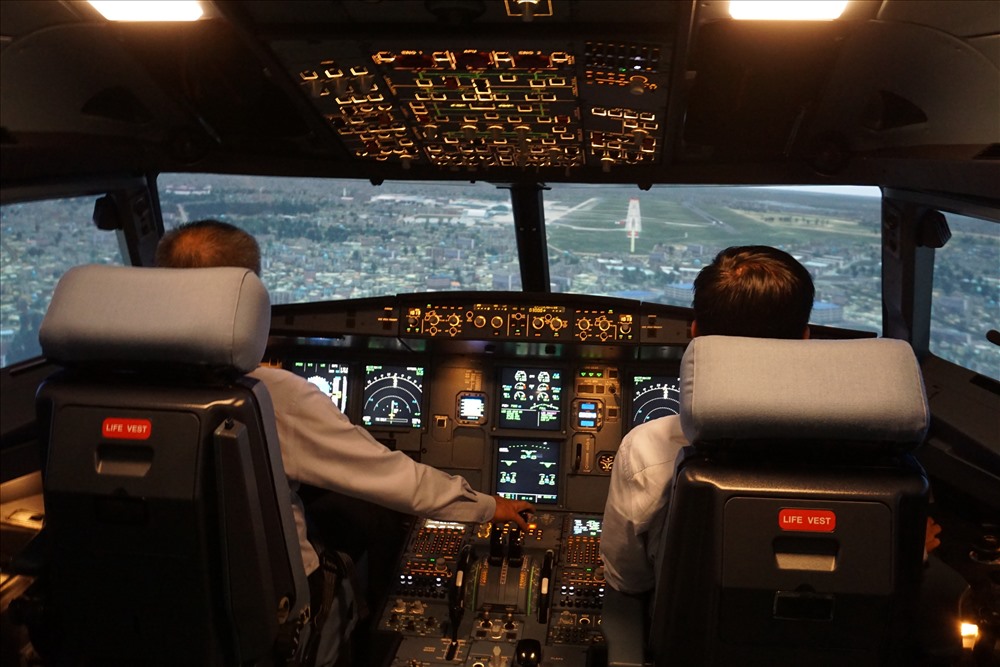
The field of ergonomics (or human factors engineering) emerged to address these issues. Scientists, engineers, and psychologists began to study how pilots interacted with their aircraft and identified ways to make controls more intuitive.
One of the most revolutionary changes was standardization. Control layouts were redesigned so that essential switches and levers were placed consistently across different aircraft models. Shape-coding was introduced, meaning different controls had distinct tactile differences—a knob for one function, a lever for another. Color-coding also became standard, ensuring pilots could quickly recognize essential instruments at a glance.
The Impact of Ergonomics on Flight Safety
The improvements were staggering. Pilot error rates dropped, accidents caused by misidentification of controls were significantly reduced, and overall flight safety increased. Modern cockpits now integrate heads-up displays (HUDs), intuitive instrument panels, and automation to further support pilots and reduce workload.
Even commercial aviation adopted ergonomic principles. Ever noticed that every Boeing 737 or Airbus A320 cockpit looks nearly identical? That’s no accident—it’s a direct result of human factors engineering ensuring that pilots transitioning between aircraft don’t need to relearn critical controls.
Beyond Aviation: Ergonomics Everywhere
The success of ergonomics in aviation led to its adoption in countless other industries. Car dashboards, medical equipment, workplaces, and even smartphones have all been influenced by the same principles that saved pilots’ lives.
Today, pilots still undergo extensive training, but they now work in environments designed to support their natural cognitive and physical abilities rather than work against them. Thanks to the science of ergonomics, we no longer expect even the most skilled professionals to battle against bad design.
So next time you board a plane, remember this: The reason your flight is so smooth isn’t just because of a skilled pilot—it’s also because someone, somewhere, made sure that their job wasn’t needlessly difficult.
You might have missed many other fascinating pieces of information, follow Maybemiss.com to stay updated on things that may be old but feel incredibly new!
Ergonomics and Human Factors: Optimizing Work Environments for Humans
Ergonomics, also known as Human Factors, is an interdisciplinary scientific field that focuses on studying the relationship between humans and their working environment. The primary goal of this field is to design tools, equipment, and workplaces that align with human capabilities and limitations to enhance productivity, ensure safety, and promote worker well-being.
Key Areas of Research in Ergonomics:
Physical Ergonomics: This area focuses on human physical characteristics such as size, shape, and movement capabilities. Research in this field helps design tools and equipment that fit users properly, minimizing the risk of injury and fatigue.
Cognitive Ergonomics: This field studies psychological processes such as perception, memory, and decision-making. The goal is to design systems and workflows that help workers process information efficiently, reducing errors and mental stress.
Organizational Ergonomics: This area focuses on optimizing organizational structures, policies, and work processes. It includes job design, human resource management, and improving communication within organizations to enhance efficiency and employee satisfaction.
Applications of Ergonomics in the Workplace:
Designing Tools and Equipment: Using anthropometric data to create tools that match users’ body sizes and shapes, reducing the risk of injury and improving work efficiency.
Workstation Layout Optimization: Arranging desks, chairs, computer screens, and other equipment to ensure comfortable working postures, reducing muscle strain and fatigue.
Developing Work Processes: Designing user-friendly processes and interfaces that minimize errors and increase work efficiency.
Training and Education: Providing knowledge about proper working postures, safe lifting techniques, and correct equipment usage to prevent injuries.
Applying ergonomic principles not only improves worker health and safety but also brings economic benefits to organizations by reducing workplace accidents, increasing productivity, and enhancing work quality.
Research on natural working environments within Ergonomics and Human Factors plays a crucial role in understanding how humans interact with their surroundings. This knowledge enables organizations to design and adjust workplaces to meet workers’ needs and capabilities, creating a safer, more efficient, and more comfortable work environment.
Discussion about this post